Manure, Environmental Impact, and Soil Health: Technologies, Application, and Benefits
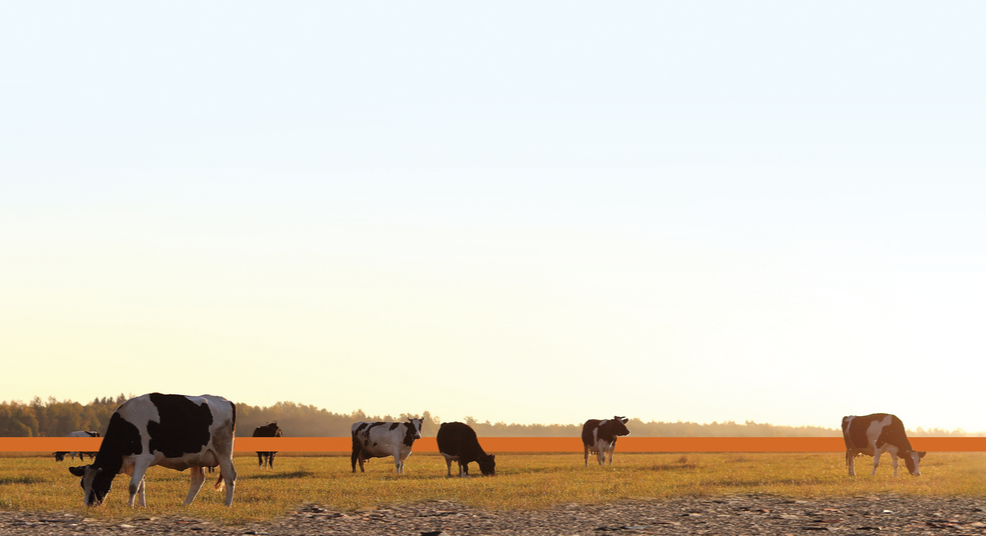
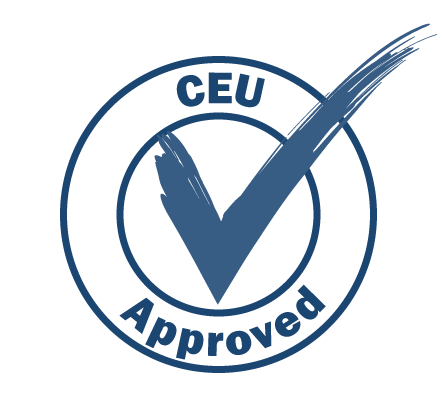
This is the fourth article in our series on soil health and greenhouse gas emissions on U.S. dairies associated with crop production. In this article, we’ll look at innovative manure products that might help dairy farmers better manage their manure resources and answer some key questions. Earn 1 CEU in Sustainability by reading this article and taking the quiz at https://web.sciencesocieties.org/Learning-Center/Courses.
Abbreviations: BAU, business-as-usual; DAF, dissolved air flotation; DSWR, Dairy Soil & Water
Regeneration; GHG, greenhouse gas; LWR, livestock water recycling; RMS, recycled manure solids. Manure is almost a perfect food for plants and an excellent soil amendment; therefore, it has been the preferred fertilizer for livestock producers for hundreds of years. It contains all 17 nutrients required for crop growth as well as valuable soil-building organic matter. As populations and demand for dairy increase, however, farmers are presented with significantly more manure challenges—what to do with it, where to put it, and how to manage its costs and environmental impacts. As such, the Dairy Soil & Water Regeneration (DSWR) project highlighted in this series is looking at innovative manure products that might help dairy farmers better manage their manure resources. We will answer a few questions about the products and processes being evaluated.
How Are Dairy Farmers Using Manure Today?
Land application has been a traditional business practice used by most U.S. dairy farmers to manage manure and preserve soil fertility. While manure is being generated and applied in its raw form to supply plant nutrients, it is becoming more challenging to maintain proper nutrient balances and control nutrient losses to the environment. This creates an uncertain regulatory environment, undermines consumer and community trust, and places a potential burden on the environment.
What Are the Environmental Impacts of Traditional Land-Applied Manure?
While land-applied manure offsets the need for some commercial fertilizers, it’s important to consider the impacts on potential greenhouse gas (GHG) emissions. When we talk about manure’s impact on the land, air, and soil, the GHGs of primary concern are methane (CH4) from manure storage and nitrous oxide (N2O) from land application. Methane production from storage occurs when the carbon-rich solids convert to methane as a result of the anerobic conditions in liquid manure storages, particularly during warm summer months. Nitrous oxide emissions are due to the high water and available carbon contents in manure that support denitrification, especially when injected in concentrated bands to prevent ammonia volatilization. In fact, N2O from land-applied manure can make up more than half of the GHG footprint of corn silage production, a significant part of a cow’s feed.
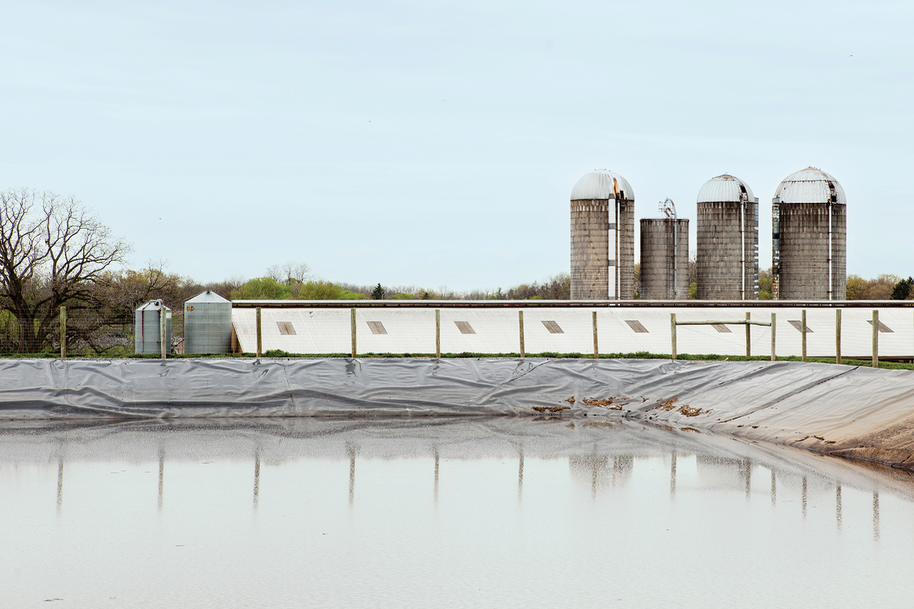
When liquid dairy manure is applied on the soil’s surface without tillage incorporation, as much as half of the nitrogen can be volatized as NH3, or ammonia, which indirectly results in significant nitrous oxide. This is an important consideration in systems with no or very little tillage to incorporate surface-applied manure. That leaves injection as the main alternative for preventing large losses of NH3, and then the trade-off is higher direct emissions of N2O.
For decades, manure was viewed more as a waste product to be removed rather than a valuable fertilizer. Historically, when field-applied at a rate that accounts for all the crop’s nitrogen needs, manure provided far above what a plant requires for phosphorus, which can result in a buildup of soil P or “legacy” phosphorus. Areas with a history of large animal concentrations, such as the hog industry in parts of North Carolina or Iowa, the poultry industry on Delmarva Peninsula on the East Coast, and historic dairy states such as Wisconsin, often have soils with very high P levels. The phosphorus in these soils may be prone to runoff and can result in eutrophication to nearby water bodies. Even using proven best management practices, losses of nutrients such as nitrate and phosphorus can only be minimized and not avoided entirely. The practicalities of storing and spreading manure often means applying far in advance of optimum nutrient uptake, thus going against the 4R principle of right timing.
How Are Technologies Transforming the Use of Manure on Dairy Farms?
Emerging technologies deliver promise by helping dairy farms balance the nutrients and reduce loss of valuable nutrients. Separating manure solids can also create a substantial decrease in CH4 emissions from storages. Removing 50% of the solids can reduce GHG emission by up to 60%. Advanced nutrient recovery technologies have opened opportunities for dairies to create energy and a long list of manure-based products, including the key nutrients—N and P, compost, bedding, custom fertilizer products, worm castings, biochar, potable water, digestate algae, humus, and struvite.
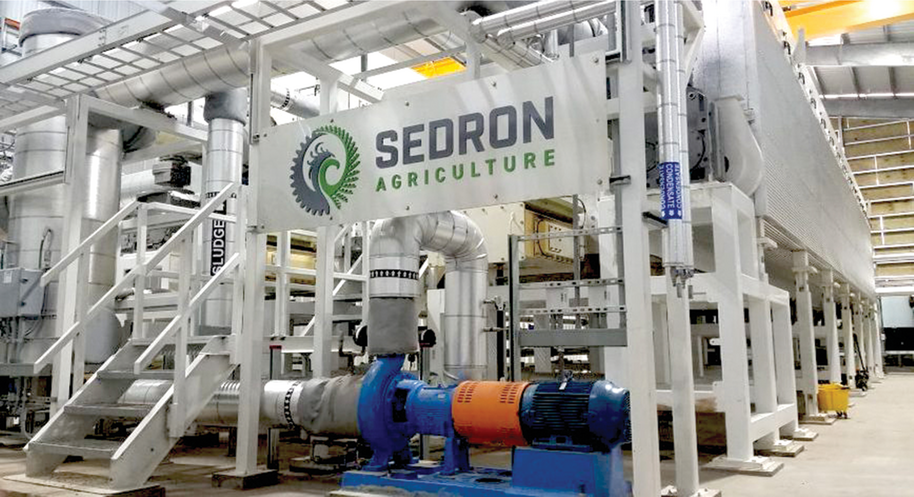
Polymer-assisted solids separation, using systems like dissolved air flotation (DAF) or other fine-solids separation systems, is a relatively mature practice for waste management in general and is now becoming more common on dairies, especially where there is a desire to export surplus P off the farm. There are several DAF systems in use for dairy manure in the U.S. The Sedron evaporative technology is in the very early stages of development, and adoption with the first commercial systems is expected to start up on two large dairy farms in 2024.
What Technologies Are Being Used for The DSWR Project?
The Dairy Soil & Water Regeneration project is evaluating solid manure-based products from advanced nutrient recovery technologies in field studies. These products are solids from dissolved air flotation and livestock water recycling (LWR) and from Sedron Technologies, an evaporation process. A key aspect of these three technologies is that most or all of the P is removed with the separated solids. In addition, DSWR is also evaluating composted dairy manure solids.
Dissolved Air Flotation
Fine solids flocculation systems, like DAF, employ chemical and physical processes to aggregate small colloidal and suspended solids into larger flocs, or masses of fine particles. In DAF systems, air, along with polymers or coagulants, is introduced into a vessel containing digested liquid dairy manure, enabling solid particles to float. These floated particles are then skimmed off, and the resulting solid fraction is subjected to mechanical solid–liquid separation and dewatering.
This process yields two main outputs: tea water, constituting approximately 80–85% of the initial mass, and a solid product comprising about 10–15% of the total mass with solids in the range of 20–25% total solids (TS). Notably, the system exhibits about 80% phosphorus and 40% nitrogen capture efficiency. The remaining nutrients are contained in the tea water, which has an estimated nutrient content of 0.5–0.5–0.1 (N–P–K). This innovative approach ensures efficient nutrient partitioning, reducing phosphorus levels in the remaining liquid fraction and allowing for the transportation of surplus phosphorus off the dairy farm while retaining valuable nitrogen and potassium resources for on-farm use.
Sedron Technologies—Varcor
The Sedron Technologies advanced vapor recompression distillation (Varcor) system is designed to process liquid waste streams containing varying solid content, ranging from less than 1 to 20%. Beyond solids separation, the Varcor system also heats, sterilizes, and distills the constituent components. This approach to treatment is applicable to many liquid waste streams, such as livestock manure, septic wastewater or biosolids, industrial liquid waste, and stillage. At the system output, the distilled reuse water is treated to desired quality standards, including those sufficient for environmental release, irrigation, reclaimed water, wastewater treatment discharge, being fed safely back to the cows. The solids produced are stable, dry, and free of pathogens, suitable for bedding or soil amendments. A concentrated ammonia solution is also produced. This ammonia-rich, stabilized liquid N contains about 10% nitrogen.
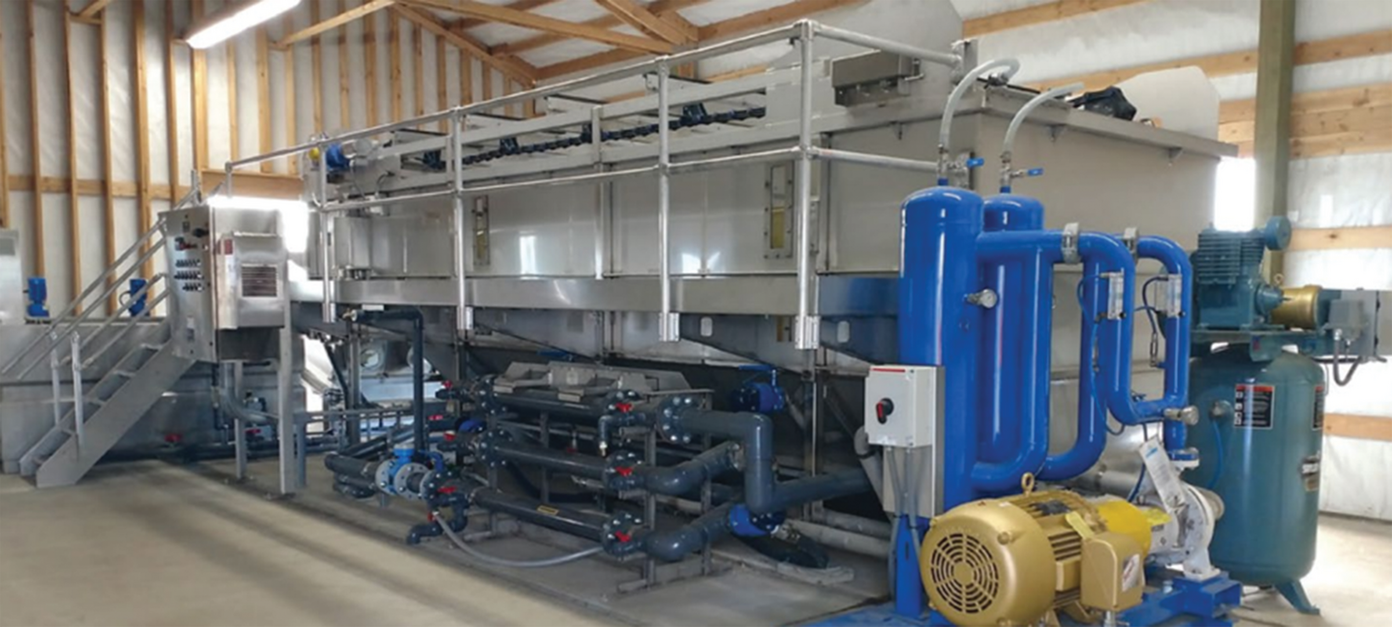
Compost
Compost is a valuable soil additive—it improves soil health, increases water retention and fertility, and reduces the need for synthetic fertilizers. The composting process involves transforming organic waste into nutrient-rich compost through controlled decomposition. This method optimizes temperature, moisture, and oxygen levels, facilitating the microbial breakdown of less stable organic matter. In the process of composting dairy manure, solid components, such as manure solids and fibers, known as recycled manure solids (RMS), are extracted from the liquid part of the raw slurry using separation technologies like slope screens, vibrating screens, or screw presses. Once separated, the RMS can be processed through various methods, including traditional windrow, air-assisted, or drum composting. The choice of composting method influences the duration required for the compost to mature.
As a result, composting reduces both odor and mass, concentrating nutrients in a smaller volume. While some ammonia is lost during composting, nitrogen is still concentrated. When compared with raw dairy manure, compost is more effectively sequestered within the soil organic matter. The resulting compost becomes a valuable soil conditioner, rich in nutrients, and is utilized in agricultural practices to enhance soil fertility and structure, fulfilling a key role in the circularity of nutrient management in dairy farming.
All three processes result in materials that have significantly higher concentrations of plant nutrients compared with traditional manure. In addition, manure can be processed on a continuous basis, avoiding dairy storage issues and the associated CH4, N20, and NH3 emissions. Lastly, manure products from advanced technologies can be more easily stored until the agronomically and environmentally optimum time of application without significant GHG emissions during storage. This is an important reason why products from the above three technologies were selected for evaluation in the DSWR project.
Are All Research Sites Using the Same Advanced Nutrient Technologies?
All dairy farms have unique designs, sizes, and regions that impact manure management collection and storage decisions. The general approach is the same for New York, Vermont, and Wisconsin where free-stall dairies with scrape manure systems are the norm. Systems of manure product and tillage system/cover crop are being compared. A business-as usual (BAU) system including broadcast liquid dairy manure incorporated with tillage and no cover crop is being compared with advanced soil health systems including broadcast application of DAF and Sedron solids or injected liquid dairy manure coupled with no-till or strip till and a cover crop. In both systems, the manure products are applied on a P basis and supplemented with commercial N as needed. Both systems include a summer corn silage crop.
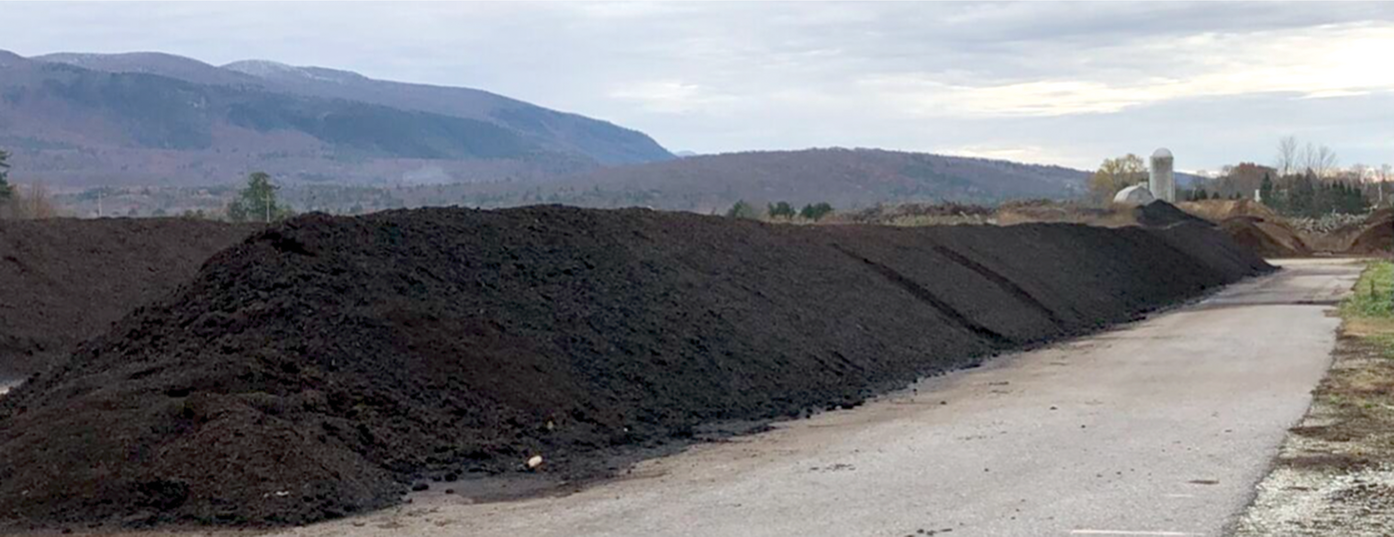
In California, the BAU system is liquid dairy manure from a flush manure system applied via flood irrigation coupled with conventional tillage. The advanced soil health system supplements flood- irrigated liquid dairy manure with dairy manure compost coupled with strip tillage and a cover crop. Both systems include a summer sorghum silage crop and a winter triticale silage crop.
In Idaho, DAF and Sedron solids applied on a P basis and supplemented with commercial N are being compared on both non-manured and heavily manured ground. All treatments involve strip till and cover crops.
In all of the above studies, a control with no N applied is included to provide a measurement of background N2O.
What Are the Challenges With Advanced Nutrient Technologies and Products Today?
There have been a lot of false starts in the development of advanced manure-based processes and products because the added value has not exceeded the added cost. The technical challenges and development costs are large. In the current environment, reduced GHG footprint is an added value that is anticipated to help offset the cost of new manure-based processes and products.
What Have We Learned So Far?
These kinds of studies must be conducted over several years to see trends. It is too early to see trends for increased carbon sequestration in soil organic matter with reduced tillage and cover crops. We are starting to see trends in less N2O from surface applications of the new manure products than from surface/incorporated and injected applications of liquid dairy manure.
A significant success has been increasing awareness that the new manure products can be a good fit for reduced-tillage systems because they don’t have to be injected or incorporated with tillage to prevent large NH3 volatilization losses from land-applied manure. Another significant success has been increasing awareness that by by-passing traditional manure storage, the new manure processes may avoid some GHG emissions from BAU storage.
One of the challenges faced so far is that, compared with conventional tillage, reduced tillage with cover crop has resulted in somewhat lower corn silage yields in the early years of the study. This is a common occurrence during the transition years of no-till or reduced tillage, especially in the northern dairy states. One question is whether the soil health benefits will start to appear in the no-till/reduced-till fields and ultimately provide equal or better yields.
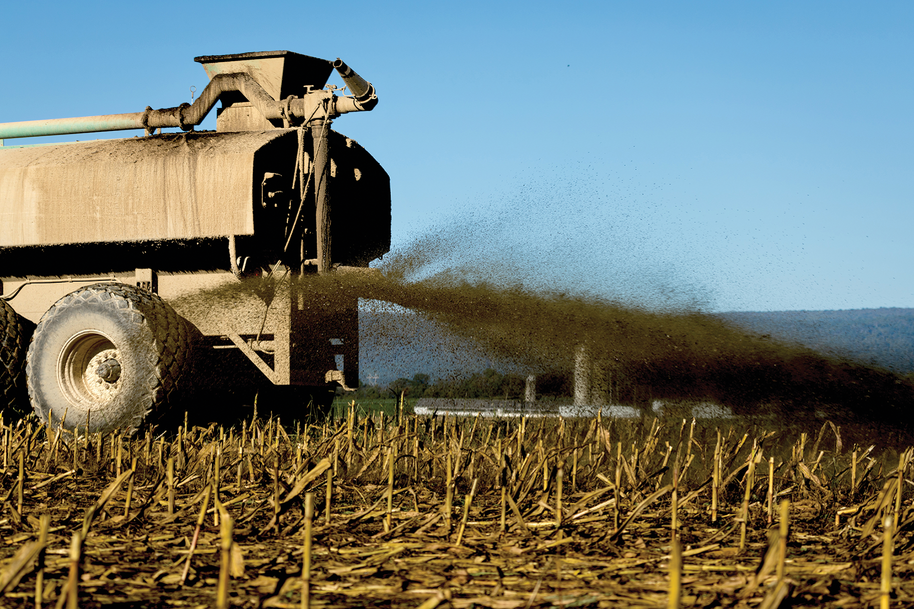
What Are Some Other Advanced Nutrient Technologies on the Horizon?
One example is vermicomposting or vermifiltration, which uses earthworms to convert biodegradable organic waste into humus-like vermicasts. Liquid dairy manure is sprinkler-irrigated onto a bed of porous organic media containing earthworms. The bed contains some aerobic microsites that convert organic N to ammonium and then to nitrate and also some anaerobic microsites that denitrify nitrate. Very little methane is produced and very little NH3 is volatilized. The end result is very low CH4, denitrification of much of the N, a vermicompost product suitable for use as a fertilizer (including for export off farm), and a liquid stream with reduced nutrient levels more suitable for recirculation and flushing and for land application on dairies with surplus manure nutrients.
Another example is the N2 Applied technology that uses plasma-arc technology to convert atmospheric nitrogen (N2 gas) to nitrogen oxides that, when added to liquid dairy manure, convert to nitric acid and lower the pH of liquid dairy manure. The lower pH should prevent methane emissions as well as denitrification of the added nitrate from stored liquid dairy manure and also prevents NH3 volatilization from surface-applied liquid dairy manure.
Do the Farms Need Any Special Equipment to Apply the Manure-Based Products?
Although the advanced solid products have significantly higher nutrient concentration than raw manure, the nutrient concentrations are still significantly lower than in commercial fertilizers. Some modification of commercial fertilizer spinner spreaders and pneumatic applicators may be required. Commercial liquid fertilizer application equipment set at relatively high volumes should be suitable for the Sedron liquid N product. For the polymer-assisted separated solids, a spreader designed for semi-solid manures, e.g., slide slingers, will be needed to apply the solids.
What Might the Future Hold for Manure as a Potential Revenue Source for Farmers?
Manure and manure-based products are excellent sources of plant nutrients. However, the relatively low nutrient concentration in traditional dairy manure, especially liquid dairy manure, limits the amount of net revenue dairy farmers can receive from dairy manure as a fertilizer source. New manure processes that result in higher nutrient concentration increase the potential for net revenue from manure products, especially if the new products qualify for the organic market and ecosystem services markets. Fractioning manure into its constituent nutrients can also allow more precise applications to better meet crop needs while minimizing losses. These technologies also allow for the mitigation of GHG emissions while still providing water quality benefits that come with storing manure.
Self-Study CEU Quiz
Earn 1 CEU in Sustainability by taking the quiz for the article at https://web.sciencesocieties.org/Learning-Center/Courses. For your convenience, the quiz is printed below. The CEU can be purchased individually, or you can access as part of your Online Classroom Subscription.
- Manure is a significant source of which greenhouse gases?
- Nitrous oxide and carbon dioxide.
- Sulfur dioxide and carbon dioxide.
- Methane and carbon dioxide.
- Methane and nitrous oxide.
- Historically, when manure was applied at a rate to account for the crop’s nitrogen needs,
- the manure did not provide enough of the plant’s required amount of phosphorus.
- the soil lost “legacy” phosphorus.
- the manure provided too much phosphorus, leading to a buildup of “legacy” phosphorus.
- the soil built up “legacy” nitrogen.
- Removing 50% of manure solids can reduce greenhouse gas emissions by
- 60%.
- 50%.
- 10%.
- 6%.
- In fine solids flocculation systems like dissolved air flotation, masses of fine particles are broken down into smaller suspended solids.
- True.
- False.
- Dissolved air flotation exhibits ___ phosphorus and ___ nitrogen capture efficiency.
- 85%, 25%
- 80%, 80%
- 80%, 40%
- 20%, 25%
- Sedron Technologies’ Varcor system can be applied to liquid waste streams, including
- stillage.
- biosolids.
- industrial waste.
- All of the above.
- Which of the following is NOT a benefit of compost?
- Reduced odor.
- Less concentrated nutrients.
- Reduced need for synthetic fertilizers.
- Reduced mass.
- Manure products from these advanced technologies can be more easily stored without significant greenhouse gas emissions during that time.
- True.
- False.
- Which advanced manure-based product can be applied with commercial liquid fertilizer application equipment set at high volume?
- The Sedron liquid N product.
- Compost.
- Vermicompost.
- Polymer-assisted separated solids.
- The new manure products can be a good fit for reduced-tillage systems because they don’t have to be incorporated with tillage.
- True.
- False.
Text © . The authors. CC BY-NC-ND 4.0. Except where otherwise noted, images are subject to copyright. Any reuse without express permission from the copyright owner is prohibited.